The requirements of implementing more stringent standards on vehicle emissions and fuel consumption have resulted in the entire automotive industry scrambling to meet these improvements. In order to reduce fuel consumption and exhaust emissions, the traditional method has been to reduce the weight of the automobile. So the aluminum alloy cylinder block instead of cast iron has evolved into a development trend. Additionally, the combustion efficiency of the engine can be remarkably improved by reducing the friction inside the engine. Therefore a new car engine technology of “cylinder Liner less” has attracted the attention of many car manufacturers.
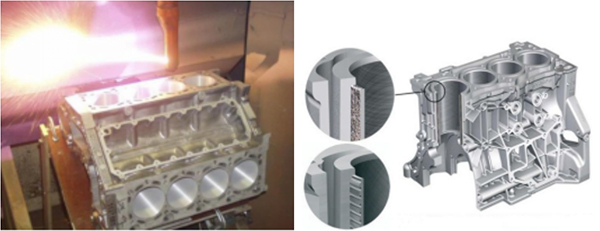
Automotive engine(s) cylinder liner less technology was accomplished by the introduction of thermal spraying technology. The application of thermal spraying is performed during the engine block production process. The spray is applied to the surface of the pretreated aluminum engine cylinder bores. The spray adds a wear resistant layer of low-carbon alloy coating to replace the traditional cast iron cylinder liner. The processing of cylinder blocks with no liners includes the following overall systems components and applications:
● the casting
● rough machining the cylinder block
● texturing-roughing up the cylinder bore
● preheating the surface
● thermal spraying
● finish machining
● finish honing
The key processes of cylinder less liner technology is performed on the coaxial surfaces (two cylinders whose cylindrical surfaces consist of the lines that pass through concentric circles in a given plane and are perpendicular to this plane) by the roughing of the cylinder surface. This is realized by:
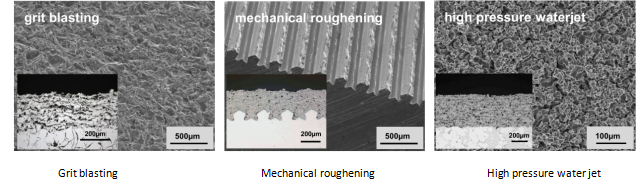
The purpose of surface roughening is required to increase the surface area to form a surface structure that allows the coating to be mechanically bonded to the surface of the substrate, increase the mechanical bite force of the coating to the substrate and further activating and enhancing the surface Material binding strength. Surface roughening is done in a variety of ways, such as grit blasting, mechanical roughing, and high-pressure water-jet roughening. Grit blasting is the most commonly used roughening treatment and applies to all metal surface roughening.
The metal surfaces can be subsequently cleaned, roughened and become highly reactive after sandblasting. This roughened surface is then cleaned with oil-free high pressure dry air before applying the spraying process.
Roughing (Surface Activation) can also be done by the use of a machine. And there are processes whereby the aluminum surface is shaped into a certain contour. This is done by use of a single-axis machining center and the use of inserted cutting tools. This is one-time processing to complete the characteristics in a cost effective approach. In the case of the older highly abrasive cast iron cylinder, excessive tool wear and tear was created often making this economically unacceptable.
High-pressure water jet roughening is only applicable to the aluminum cylinder and not applicable with cast iron cylinder. The Water jet process does not use costly abrasives. However the direct use of liquid jet on the substrate surface is only accomplished when the surface is dry. And even then the surface roughness value is relatively low compared to other processes.
Surface roughening as a key process in the non-cylinder technology directly affects the bonding strength and coating properties of the coating. Therefore, it is critical to pay attention to the surface roughening process in utilization of cylinder less cylinder block technology. Selection of the appropriate roughing method is critical in achieving the best activation of the surface and production efficiency.
Post time: May-26-2021